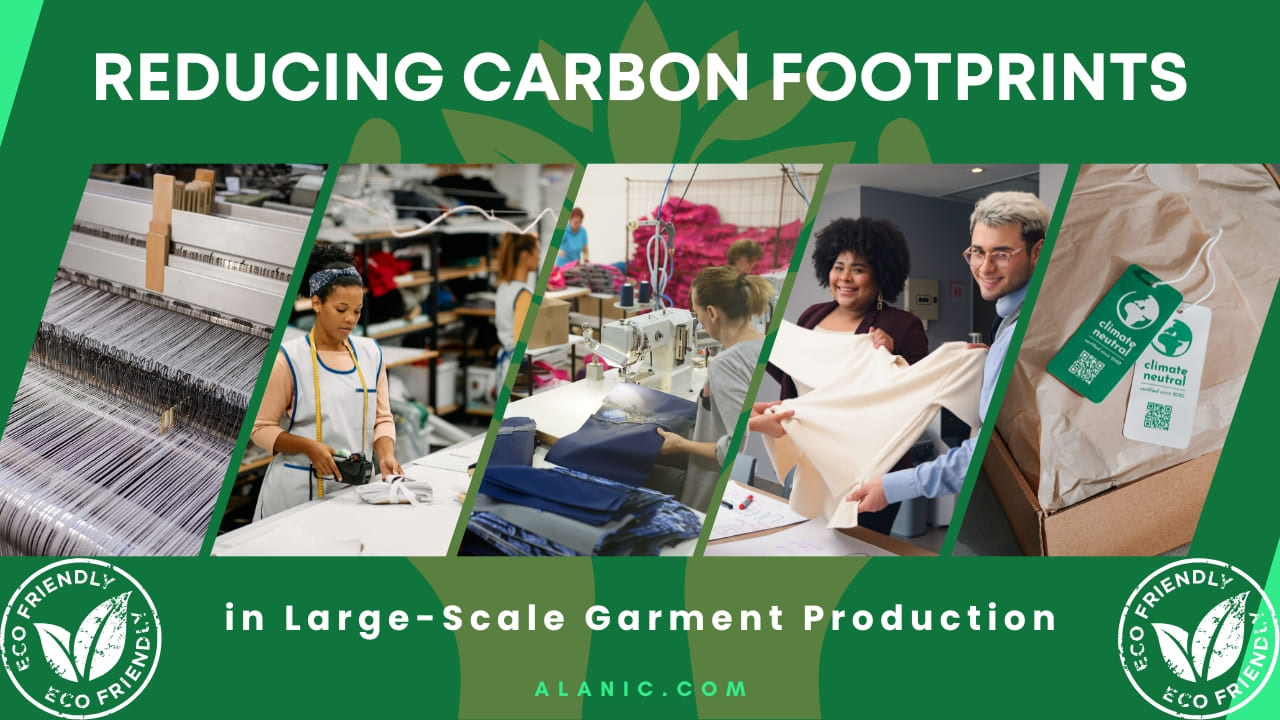
Producing garments at volume means managing more than output. Every decision—from fabric sourcing to packaging—shapes a carbon footprint that scales with the business. At a certain level, efficiency and sustainability stop being separate conversations.
In large-scale clothing production, footprint reduction becomes structural. It influences process design, supplier selection, and product planning.
The shift is no longer theoretical. It plays out daily in how materials move, how waste is handled, and how decisions get made.
Energy runs through every corner of a production floor—cutting tables, pressing units, lighting systems, and even ventilation.
Optimizing energy usage doesn’t always require major overhauls. Often, the impact begins with micro-decisions.
Factories now explore staged upgrades: replacing fluorescent lighting with sensor-controlled LEDs, aligning machinery schedules to peak-load awareness, and adjusting drying methods based on seasonal humidity.
Brands partnering with production facilities can ask simple questions early: how power loads are managed, what equipment runs overnight, and how idle time is tracked.
Answers to those questions often reveal low-effort opportunities for energy reduction.
The first environmental cost in apparel happens before production even begins.
Yarn processing, fiber blending, and material dyeing account for significant emissions long before fabric hits the cutting table.
Switching from virgin polyester to recycled blends, or opting for organic cotton over conventional, shifts the footprint closer to raw inputs.
But it only works when those materials meet the product’s demands—durability, stretch, and colorfastness.
Brands working with performancewear or athleisure lines often face a trade-off. The key is matching the product’s lifecycle with its material. Choosing a recycled option that holds up across 40+ wears typically offsets its higher sourcing cost.
Designing with lifespan in mind reduces impact more effectively than simply choosing a greener fiber.
Among all production stages, wet processing remains one of the most resource-intensive. Dye baths, chemical treatments, and heat-setting consume water, energy, and often rely on non-renewable inputs.
Even mills making strides with waterless dyeing or closed-loop systems admit the challenge of consistent application across styles and fabrics.
Manufacturers evaluating dyeing processes can review whether vendors track chemical dosage, use recycled water systems, or monitor discharge output.
These aren’t just compliance checks; they often correlate with cleaner processes overall.
Asking where the color comes from—and what’s left after it sets—is a key step in understanding material impact.
Each physical sample produced represents time, energy, transport, and material—all before a sale ever happens. Multiply that across several development rounds, and the resource cost adds up quickly.
More brands now lean on digital sampling, photo-based pattern checks, and virtual fittings to reduce the number of physical samples produced during development.
Manufacturers supporting this approach often build systems where core blocks are reused, adjustments are digitized first, and samples only go into production when fit confidence is high.
It saves material. But it also trims down lead time and cuts freight emissions across the sample cycle.
Overproduction quietly drives both financial and environmental loss.
Planning more accurately, especially in large-volume orders, can drastically reduce waste in the form of unsold product, excess trims, and warehousing costs.
Forecasting tools are one part of the answer. The other is flexibility in ordering systems.
When brands and factories align on smaller batch runs with shorter intervals, stock can be replenished based on actual sell-through.
Packaging and shipping also scale with smarter batching.
Reducing the number of partial-container shipments or mixing production lines for combined freight has become common practice in large-scale setups.
Less product in the wrong place at the wrong time means fewer emissions are burned moving them around.
Even in performance apparel—where use cases are more intense—better construction extends a product’s utility.
Double-needle stitching on high-stress seams, pre-washed fabrics to stabilize shrinkage, or better elastic retention all lead to longer product life.
A t-shirt worn fifty times instead of ten delivers lower emissions per wear, regardless of the original fabric.
Designers and manufacturers working together on construction specs can focus on reinforcements, pattern alignment, and durability in fabric blends to lengthen the usable life of each piece.
The most sustainable garment is often the one that doesn’t need replacing next month.
While the product receives most of the attention, packaging decisions can make quiet gains in sustainability.
Switching to paper wraps, reducing unnecessary labeling, or combining items into single packs can cut packaging waste by volume and material use.
For larger shipments, optimizing box dimensions to match product volume minimizes air freight space.
Small changes like flat-packing garments, folding to reduce bulk, or using thinner protective sleeves still deliver protection without excess.
Many brands now view packaging design as part of product development, not something tacked on at the end.
Clear reporting builds trust between manufacturers and brands.
Certifications from organizations like OEKO-TEX, WRAP, or GRS help align partners on environmental standards without constant auditing.
But paperwork alone doesn’t solve emissions. What matters is how often the process behind the label gets reviewed—and whether feedback loops exist when gaps are found.
Manufacturers working at scale now often share monthly or quarterly production data tied to efficiency metrics, material usage, and yield percentages.
Brands that request and review these metrics position themselves to make real adjustments at the planning level.
Transparency makes sustainable improvements trackable and real, not just symbolic.
Carbon reduction in garment manufacturing doesn’t rely on one fix. It comes from a network of small decisions, repeated consistently across systems.
At Alanic Wholesale Clothing, we’ve worked with brands that care about more than output speed. Some ask about fabric origin. Others ask how sampling is handled. And many are now rethinking what makes a product “finished”—not just in look, but in waste.
As manufacturers, we see sustainability less as a campaign and more as a responsibility embedded in the process of how we source and how we cut, what we build toward.
The pressure to lower emissions will only grow. The businesses that take it seriously now will be the ones leading—not just reacting—later.